What is Sustainable Quality Management (SQM)?
Sustainable Quality Management recognizes that there are finite social, financial, and environmental resources to deliver a high-quality project. It aims to maximize sustainable value; this translates to delivering the best possible high-quality product or service with minimum financial and environmental costs along with adding positive social value at every opportunity (Quality Gurus, unknown). SQM has many key principles, in order to achieve ESG goals. Some of these principles are, customer focus, innovation, adaptation…etc. However, the umbrella that covers all those principles is Continuous Improvement.
What is Continuous Improvement?
The idea behind this principle is to continuously seek ways to improve the final outcome. This method involves feedback from suppliers, clients, staff…etc. If there’s a problem that occurred, i.e., a certain unexpected failure in a process or product, the issue must be addressed. This is a system to improve the quality of processes and results over time.
A continuous improvement strategy entails the creation of rigid guidelines, policies or procedures, or any sort of process within an organization that encourages to keep the focus on improving how tasks are done on regular basis. This could be by intending on achieving larger process improvement over time. The secret of this concept is taking initial data and comparing it to other data that has been collected after adjustments and changes have been made, this will identify if the solutions and changes are effective or not, for example, reduce accidents on site for workers.
- Metrics need to be recorded prior to any changes made
- Chosen process, i.e. policies and procedures should be put into place, such as, mandating Health and Safety attire to be worn at all times on site.
- Metrics of the number of injuries on site can then be measured and compared to the initial number taken before implementation of Policies and Procedures.
Continuous Improvement constantly allows new solutions to be carried out to further improve results. This constant improvement methodology can be implemented by the PDCA model.
Deming Cycle: PDCA Model
The PDCA cycle is a continuous improvement loop which consists of planning, doing, checking and acting. It’s a methodology that provides a simple approach for solving problems and managing change. The model is very useful in testing measures of improvement before updating procedures and strategy in an organization. As shown in Figure 1, each step is built on the step prior to it, and then feeds into the next one. The PDCA model could be used to implement continuous improvement in any system. Each step is explained below.
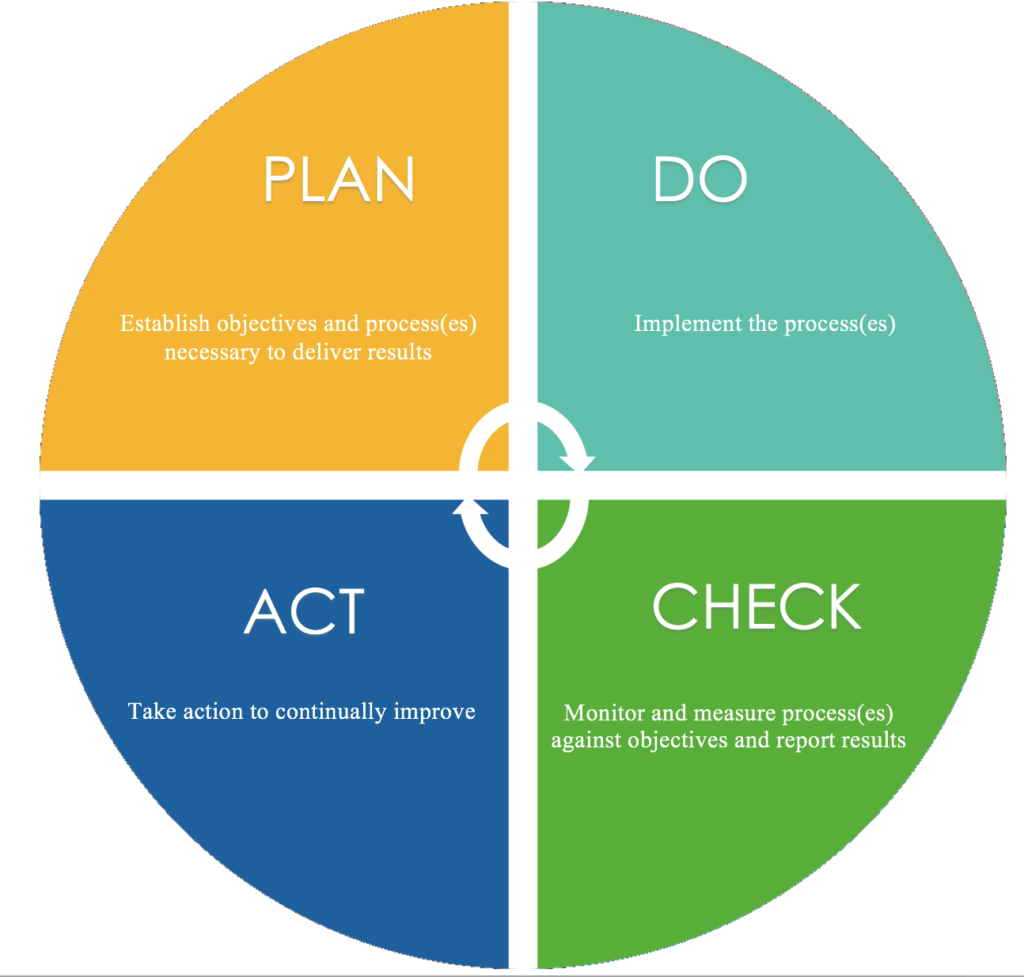
This is when teams are required to measure current standards and brainstorm ideas to create improvement and decide on how it should be implemented. The end product of this step is the plan of action.
The plan that was created in the previous step will be now implemented. This includes changing the existing process, and adding controls to avoid potential problems. This will all be created around the new objectives set.
New measurements are taken in this step to compare to ones taken earlier. This step will identify if any improvements took place. Results must be analyzed and preventive and correction action need to be done, i.e. adjustment of policies or procedures.
All data from change is then analyzed to determine whether the change will become permanent or needs further adjustments. After that, the cycle is then repeated to implement the new change.
How can Continuous Improvement be used?
Continuous Improvement is important for SQM because it allows organizations to adapt and evolve in response to changing circumstances and stakeholder expectations. Continuous Improvement can be used in various ways to enhance processes, products, and overall performance. Below are a few examples:
Continuous Improvement methodologies, such as PDCA, can be applied to identify and eliminate inefficiencies in workflows. By regularly reviewing and refining processes, organizations can streamline operations, reduce waste, and improve productivity.
Continuous Improvement fosters innovation by encouraging ongoing evaluation and enhancement of products or services. Through customer feedback, market research, and data analysis, companies can identify areas for improvement and make iterative changes to meet evolving customer needs and preferences.
Continuous Improvement is closely linked to quality management systems. By implementing feedback loops, conducting regular audits, and analyzing performance metrics, organizations can identify and address quality issues promptly. This leads to improved product reliability, customer satisfaction, and brand reputation.
Continuous Improvement initiatives involve employees at all levels, empowering them to contribute ideas and suggestions for improvement. This not only fosters a culture of innovation but also enhances employee engagement and satisfaction. Employees feel valued when their input is considered, leading to increased motivation and productivity.
Continuous Improvement helps organizations deliver exceptional customer experiences. By actively seeking customer feedback, analyzing customer journeys, and implementing improvements based on insights, companies can enhance satisfaction, loyalty, and retention rates.
Overall, Continuous Improvement is a powerful approach that enables organizations to adapt, innovate, and stay competitive in a rapidly changing business landscape. It promotes a culture of learning, collaboration, and ongoing growth, leading to improved efficiency, effectiveness, and customer satisfaction.